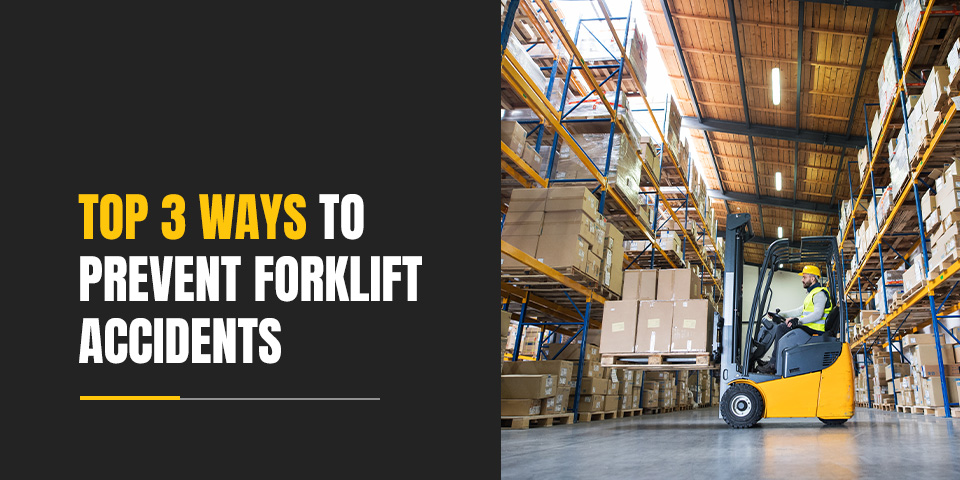
Forklifts are highly valuable to warehouse operations, and establishing comprehensive protocols to promote safety is key to maximizing their benefits. In 2021 and 2022, the National Safety Council (NSC) recorded 15,480 missed work cases (DAFW) due to forklift injuries alone. Understanding the best practices and prioritizing proactive measures to protect your workers is essential.
Explore our top tips for preventing forklift accidents and ensuring the safest operation.
1. Proper Forklift Training and Certification
Forklifts, or industrial counterbalance lift trucks, carry heavy loads and are incredibly powerful machines. Their immense weight and lifting potential require a trained, responsible hand to control safely, so only certified forklift drivers may operate them in the United States.
Certifications, evaluations and reevaluations are an employer’s responsibility. The Occupational Safety and Health Administration (OSHA) mandates all staff working with powered industrial trucks like forklifts fulfill certain training requirements.
Comprehensive Training Programs
New forklift drivers must learn to recognize and avoid potential hazards, gauge load capacity and react to emergencies. Formal education and practical training are two crucial aspects of forklift certification because drivers need knowledge and experience before getting behind the wheel. Work with a reputable operator trainer who does on-site training aligned with OSHA regulations for proper employee certification.
In lift truck operator training, drivers learn important skills such as how to:
- Start, accelerate, steer, brake, reverse, stop and secure the vehicle safely.
- Navigate blind spots, uneven surfaces, inclines and obstacles.
- Lift, move, stack and lower different load types using forks and attachments.
- Respond to tip-overs, collisions or mechanical failures.
- Wear appropriate personal protection equipment (PPE).
Regular Refresher Courses
OSHA also requires all forklift drivers to be evaluated at least once every three years and do refresher training after every accident or near-miss. These strict rules help keep operators up-to-date with newer lift truck models and regulations, iron out corner-cutting habits and reinforce proper safety standards.
Simulation Exercises
Training should always include simulations of potentially hazardous situations so forklift drivers are best prepared for every warehouse scenario.
Simulations can be done virtually or in a safe setting by professional trainers and should address common obstacles forklifts may encounter, such as:
- Overhead clearance, including doorways, pipes, lights and sprinkler systems.
- Rules for passing, communicating with and staying aware of pedestrians.
- Adjusting loads to better distribute weight between the front and back of the vehicle.
- Lifting coworkers safely using aerial platforms or cages — never on loose pallets.
- Refilling fuel tanks, replacing compressed gas tanks or recharging the forklift’s battery.
2. Regular Forklift Maintenance and Inspections
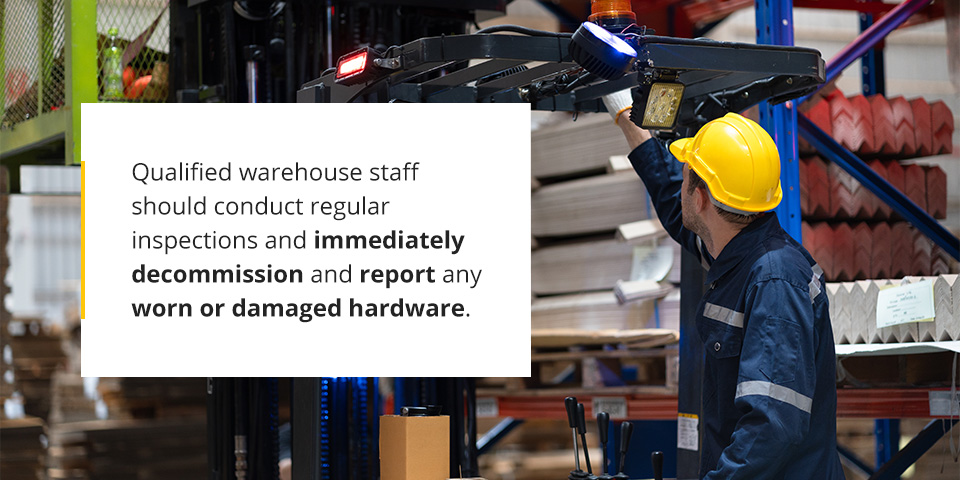
Even the most competent lift driver cannot ensure safe load transportation if their vehicles, passageways and equipment are improperly maintained. Qualified warehouse staff should conduct regular inspections and immediately decommission and report any worn or damaged hardware. To ensure your operators, vehicles and materials are safe, conduct these vital procedures:
Scheduled Maintenance Checks
Forklifts require regular maintenance to operate efficiently and safely. Professionals recommend performing preventive maintenance on newer forklifts every 250 to 300 hours. Older models, heavily used vehicles and trucks used in damp or otherwise challenging working conditions should receive preventive maintenance more frequently as they are at higher risk for wear and tear.
Daily Pre-Shift Inspections
OSHA requires that operators inspect their forklifts before and after each shift if they operate around the clock. Forklifts used sporadically still require daily inspection before use. Operators must conduct two critical inspections:
- Pre-operation inspections: With the forklift turned off, check fluid levels, tire pressure, fork condition, finger guards, visible cracks and other potential defects.
- Operation inspections: When the engine is running, check the horn, lights, steering, brakes, attachment, hoist and lowering control and other mechanisms.
Prompt Repairs
If an operator or inspector does find damage, they should immediately stop using the forklift and notify a supervisor. Supervisors should then contact a professional to repair or replace the broken part. Only certified technicians should conduct repairs on industrial lift trucks, and you should always work with the forklift manufacturer or an official dealer for the most reliable, efficient results.
3. Comprehensive Forklift Safety Protocols and Communication
Warehouses are busy, productive spaces filled with heavy machinery, stacked loads and many workers, your facility must optimize them for structural and organizational safety. By prioritizing clear communication, a rigid set of rules and adherence to OSHA guidelines and regulations, you can better protect your workplace against forklift accidents.
Clear, Bold Signage
Warning signs are excellent ways to inform and remind employees about preventing forklift accidents. These signs are imperative even if all your workers are well-trained and experienced. All signs should have their meanings explained to employees and visitors upon first arrival, the signs should be readable from at least 5 feet away, and their central message should be in pictures, written text or both. OSHA-regulated signs include:
- Danger signs: Danger signs are red, white and black. They flag extreme, potentially life-threatening spaces such as flammable fuel refilling stations and forklift traffic areas.
- Caution signs: Yellow and black caution signs indicate a moderate threat, such as low overhead clearance, wet floors, or instructions to wear PPE.
- Safety Instruction signs: Safety instruction signs are white, black and green and usually list several critical safety guidelines, such as how to react to an emergency.
Good Staff Communication
Active, direct communication saves lives in a warehouse setting.
Although forklift operators must give pedestrians the right of way, clear coordination and alertness are everyone’s responsibility. Some communication tips for forklift drivers on shift include:
- Honk the horn before blind turns and entryways.
- Use a backup alarm and lights when reversing.
- Signal for pedestrians to clear a path for the forklift.
- Instruct pedestrians not to stand under the forks.
A Safe Warehouse Environment
Your warehouse needs to be forklift-friendly to maximize safety. Machinery refueling stations must have proper ventilation, clear inclines and vertical drop markings, adequate temperature-controlled, and pathways clear of debris and clutter.
Keep forklift and pedestrian paths as separate as possible to minimize collision risk. Always ensure fire extinguishers and first aid kits are readily available.
The Importance of Forklift Accident Prevention
Forklift accidents can place operators and pedestrians at risk of injury or fatalities. Improper operation can also result in damage to valuable materials and structures or the forklift itself.
Adequate on-site safety measures protect employees’ lives and promote a better, more productive working environment for everybody. These measures enhance your warehouse’s reputation and bottom line. Investing time and energy in robust safety procedures and regular maintenance is key to your business’s success.
Enhance Warehouse Safety With Operator Assistance Technology
Warehouse operators can use innovative digital solutions to help fortify the safety of their employees and assets. Top industrial equipment manufacturers offer sensor-connected software that helps forklift drivers by:
- Heightening operator awareness with audible and visual alerts.
- Tracking the vehicle’s load and stability.
- Adjusting hydraulic functions to prevent tipping and load pitching.
- Monitoring obstacle and pedestrian proximity using tags.
- Using LiDAR sensors to assess the operator’s surroundings.
- Automatically limiting speed in high-risk zones.
- Sensing the vehicle’s location in real time.
Technological solutions help reduce the risk of human error, one of the most critical causes of occupational accidents. With these intelligent tools onboard, forklift drivers are far better equipped to navigate warehouses safely and efficiently. The Hyster Reaction™ technology package and Yale Reliant™ operator assistance tool are two examples of today’s industry-leading safety suites.
Trust Burns Industrial Equipment With Your Forklift Safety and Repairs
Since 1972, Burns Industrial Equipment has supported businesses with their fleet management, industrial equipment procurement, repair and maintenance needs.
We’re an authorized Yale and Hyster dealer and offer operator training, parts and warehouse solutions from our locations in Western Pennsylvania, Northeast Ohio and West Virginia.
Contact us online to maximize your warehouse safety and optimize your forklift fleet today.
